Public Funded Projects
Research activities dealing with subjects of public interest (e.g. emission reduction or renewable energy sources) are supported by public funding:
PRIN 2020- H2ICE: development of a hydrogen fueled hybrid powertrain for urban buses
The H2ICE project aims at the development of an innovative hybrid powertrain for urban buses, based on a hydrogen fueled Internal Combustion Engine (ICE), capable of providing a zero CO2 and near zero criteria pollutant emissions solution, with a significant cost saving (up to one order of magnitude at time of writing) if compared with other zero emissions powertrains, such as Fuel Cell Electric Vehicles (FCEVs).
The project will focus on the development of a new generation of hydrogen fueled ICEs, designed to be operated with ultra-lean mixtures, thus achieving extremely low NOx emissions (below 0.05 g/kWh), along with unprecedented efficiency values (above 42%). These figures make these new engines extremely promising candidates for urban buses applications, for which a quite limited range is typically requested, and tank refueling is not an issue, since it is possible for captive fleets to centralize the fuel stations in a single hub. Moreover, these already outstanding efficiency values could be further enhanced by the synergic combination with hybrid propulsion technologies, that are particularly suitable for urban buses applications, for which series hybrid could significantly benefit from energy recovery through regenerative braking, as well as from a substantial downsizing of the ICE, since vehicle acceleration performance can be decoupled from engine power output.
However, the full exploitation of the potential of such a hybrid powertrain requires a substantial enhancement of the state of the art, since several challenging issues have to be addressed. In particular, the control of the fuel injection and of the combustion process is extremely challenging, due to the high risk of backfire in case of port fuel injection and to the complexity of managing mixture formation through the supersonic flow of the gaseous fuel in case of direct injection, as well as to the need of identifying a “sweet spot” in the ultra-lean combustion region which could allow extremely low NOx emissions along with high combustion efficiencies.
Specifically designed combustion diagnostic techniques will therefore be developed, for knock and misfire detection. Moreover, to further enhance the engine efficiency, different Waste Heat Recovery (WHR) systems will be carefully scrutinized, including both Organic Rankine Cycle (ORC)-based recovery units as well as electric turbo-compounding. Finally, a Selective Catalytic Reduction (SCR) aftertreatment system will be developed to bring already low engine-out NOx to near-zero emissions levels. At powertrain level, advanced energy management strategies, fully exploiting V2X communication, will be developed.
In conclusion the performance of the whole hybrid hydrogen fueled propulsion system will be assessed on a virtual test rig over several Real Driving Emission (RDE) tests, targeting to achieve a hydrogen fuel consumption of about 0.1 kg/km, which can successfully compete with a FCEV at a much lower cost.
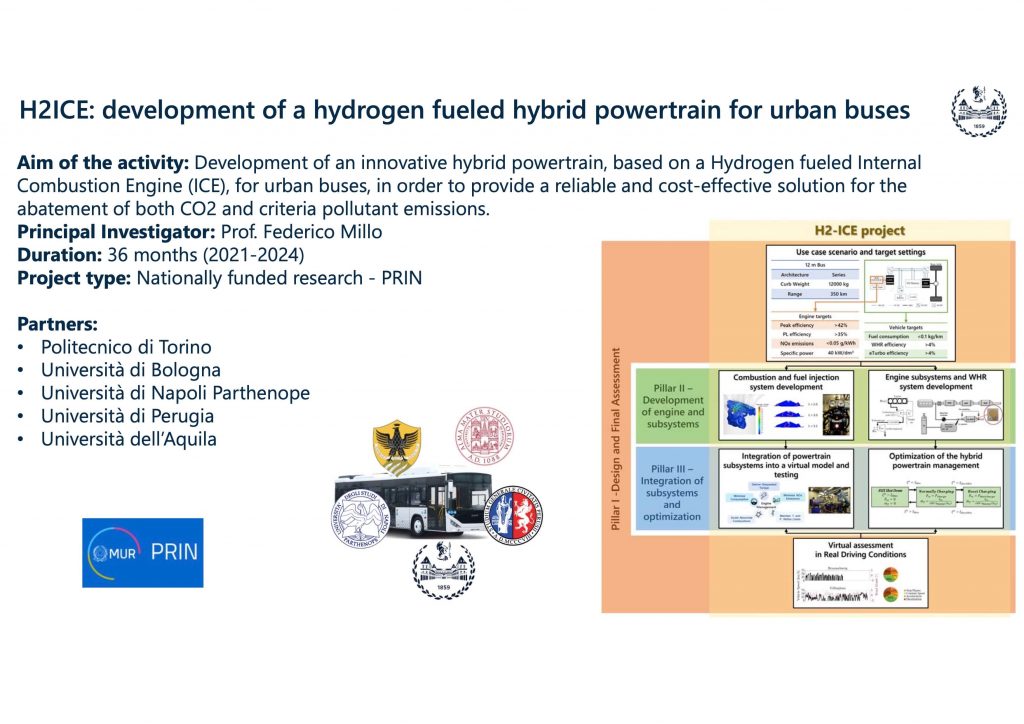
MISE H2-ICE: Hydrogen-fuelled internal combustion engine
The H2ICE project is an ambitious initiative that aims to develop two innovative hydrogen-powered engine platforms: a monofuel engine and a dual-fuel one. These engines are designed for application in both stationary systems, such as combined heat and power (CHP) units, and mobile platforms, including heavy-duty vehicles like buses, trucks, and pick-ups, as well as maritime transport. The overarching goal of the project is to offer a scalable, cost-effective, and sustainable alternative to diesel engines and more expensive zero-emission technologies like fuel cell electric vehicles (FCEVs).
At the heart of the project is the development of internal combustion engines capable of running on hydrogen while achieving ultra-low pollutant emissions and extremely high thermal efficiency. The engines will be designed to operate with ultra-lean air-fuel mixtures, allowing for NOx emissions lower than 0.05 g/kWh and thermal efficiency above 42%. These figures make hydrogen ICEs a promising solution for urban transport and stationary energy generation, particularly because of their potential to integrate well with hybrid systems. In urban bus applications, for instance, hybridization allows for energy recovery during braking and a reduction in engine size, thus improving overall system efficiency and performance.
However, achieving these ambitious targets poses significant technical challenges. Managing hydrogen injection and combustion in ICEs requires advanced control strategies to avoid issues like backfire or poor mixture formation. The project addresses these challenges by developing innovative diagnostic tools for detecting knock and misfire and by identifying the optimal operational “sweet spot” in ultra-lean combustion.
The H2ICE project is coordinated by Dumarey Automotive Italia S.p.A., a company with a strong legacy in engine development and innovation, and now part of the Belgian Dumarey Automotive Group. The company is supported by two key partners: the Politecnico di Torino and TecnoGen S.p.A. The university contributes through five specialized research units from the departments of Energy (DENERG) and Applied Science and Technology (DISAT), focusing on combustion science, emissions aftertreatment, materials compatibility, and life cycle assessment. TecnoGen, an internationally recognized manufacturer of generator sets and CHP units, will lead the adaptation of the hydrogen ICE into energy production systems, leveraging its patented FUSTEQ technology to deliver low-noise, energy-efficient solutions.
With a planned duration of 36 months, the project is funded through Italy’s “Accordi per l’Innovazione” program under the Ministry of Enterprises and Made in Italy.
Ultimately, the H2ICE project represents a strategic step forward in the transition toward low-emission mobility and power generation. By combining advanced engineering with applied research, it offers a promising route to decarbonize key sectors of transport and energy while maintaining the reliability and the cost-effectivness of internal combustion engines technology.
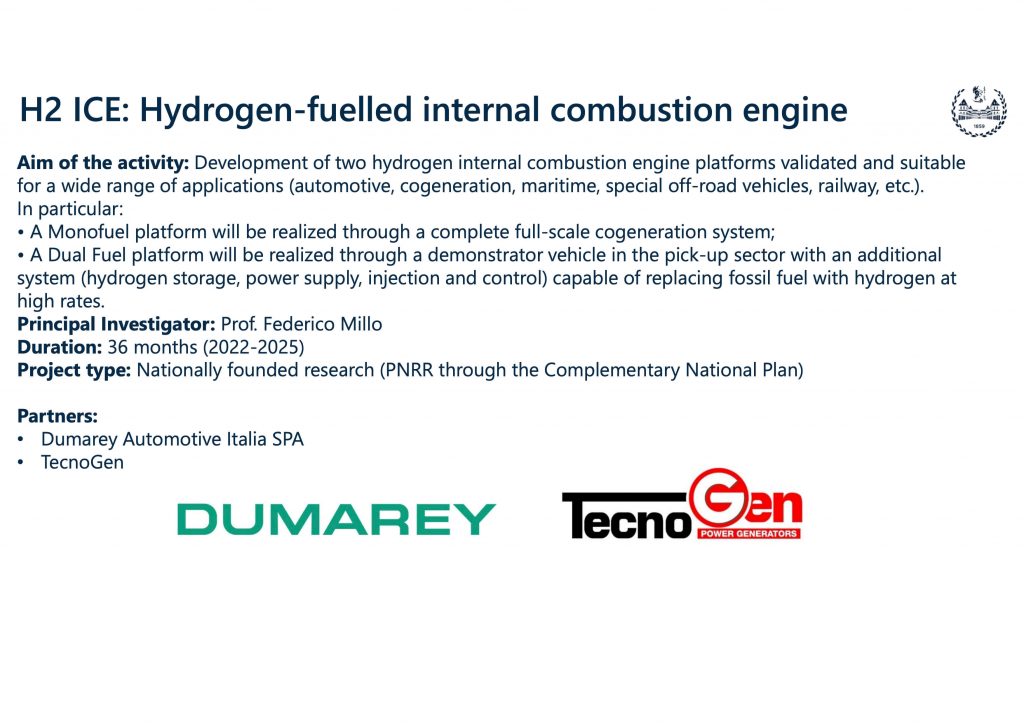
MISE – HERO: Hydrogen European Research Opportunity
This industrial research and development project led by Westport Fuel Systems Italia S.r.l. focuses on the development of innovative hydrogen-based propulsion systems to support the decarbonization of the transport sector. The initiative is part of the broader national strategy for energy transition and is co-funded by the Italian Ministry of Enterprises and Made in Italy under the “Accordi per l’Innovazione” program (D.M. 31/12/2021).
The project involves a strong partnership between three key players: Westport Fuel Systems Italia, the Politecnico di Torino, and Dumarey Automotive Italia S.p.A.. Each brings complementary expertise to the initiative. Westport, a global leader in alternative fuel systems, contributes extensive industrial know-how and a broad portfolio of components and technologies, including its high-pressure direct injection (HPDI) systems and hydrogen components. The Politecnico di Torino, one of Europe’s top engineering universities, will contribute through three specialized research units from the Departments of Energy (DENERG) and Applied Science and Technology (DISAT). These units will focus on hydrogen combustion processes, fuel cell optimization, and material compatibility studies. Meanwhile, Dumarey Automotive Italia S.p.A., with a long tradition in engine and powertrain innovation, will bring its engineering capabilities, prototyping facilities, and testing infrastructure into the collaboration.
The project’s overarching objective is to design and validate hydrogen-powered propulsion systems suitable for various mobility applications—ranging from light-duty to heavy-duty vehicles. The approach is twofold: on one side, the project aims to enhance internal combustion engines fueled by hydrogen, improving their injection, combustion control, and performance under ultra-lean and HPDI conditions. On the other, the consortium will also work on optimizing hydrogen fuel cell systems, with a particular focus on the design of the anodic circuit and the integration of efficient, durable components.
One of the core technical challenges lies in managing the interaction between hydrogen and engine components. This includes studying the mechanical behavior of materials in contact with hydrogen under different pressures and temperatures, identifying the most reliable and cost-effective solutions. The DISAT research group, with a strong background in micro- and nano-materials, will play a key role in these studies, particularly in characterizing and optimizing PEM fuel cell components for long-term performance.
Furthermore, the project will produce complete demonstrators and integrate the developed technologies into real-world testing environments. The advanced facilities at Dumarey Automotive Italia S.p.A., including hydrogen-compatible test cells and fuel cell testing benches, will be instrumental in validating the results.
The scope of the project, the level of institutional and industrial engagement, and the infrastructure involved positions the initiative as a flagship project in Italy’s hydrogen and clean mobility roadmap.
With a planned duration of 36 months, the project is funded through Italy’s “Accordi per l’Innovazione” program under the Ministry of Enterprises and Made in Italy.
In summary, this project represents a major step forward in hydrogen mobility. By combining academic research, industrial engineering, and technological innovation, the consortium seeks to provide practical, efficient, and scalable hydrogen solutions for the automotive industry—helping meet both environmental targets and market demands for low-emission transport.

Phoenice: PHev towards zerO EmissioNs & ultimate ICE efficiency
The PHOENICE project aims to unlock the full potential of plug-in hybrid vehicles by optimizing their performance to significantly reduce both fuel consumption and pollutant emissions under real-world driving conditions. To achieve this, the project is developing a highly efficient powertrain system that will reach Technology Readiness Level 7 (TRL 7). Key innovations include a gasoline engine with a peak efficiency of 47%, advanced energy management for the entire vehicle, and a fully integrated, state-of-the-art exhaust aftertreatment system. Throughout the development process, particular attention is given to ensuring the solutions are cost-effective, scalable for industrial production, and designed to minimize both economic and environmental impacts.
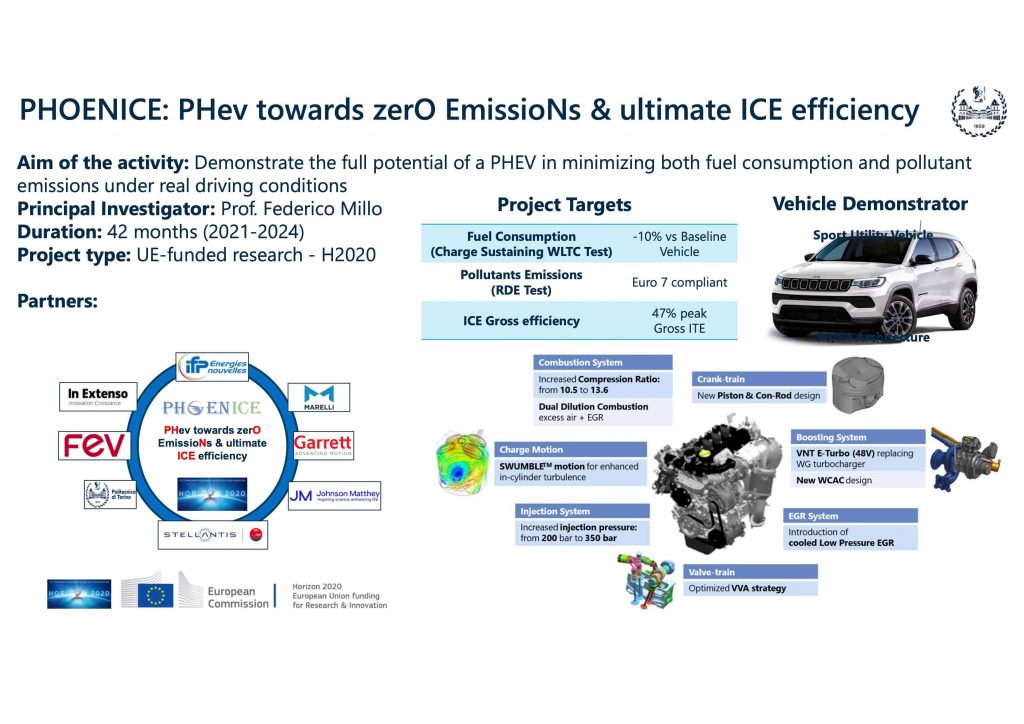
Public Funded Project Archive
The project “Development of a new generation of powertrain for hybrid and electric vehicles”, in collaboration with FEV Italia, is a part of a wider research investigation on future technologies for CO2 emission reduction. The project is currently focussing on:
• Detailed experimental campaign for each powertrain sub-system
• Development of analytical models for hybrid powertrain performance prediction
• Energy management strategy definition
The TIVANO project (Italian acronym for Innovative Technologies for New generation General Aviation Aircrafts) funded by the Italian Minister of University & Research (MIUR) within the framework of the CLUSTER projects has the target to develop new technologies for general aviation aircrafts and UAS (Unmanned Aircraft Systems). In details:
• Diesel-Electric hybrid Powertrains
• New low-cost composite materials
• Electric brake-by-wire systems
The project tasks carried out in the e3 lab will focus on the first item developing together with other Departments of the Politecnico the first diesel-electric hybrid powertrain system for aircrafts. Nowadays hybrid powertrain systems for aircrafts are becoming interesting since, even if does not actually exist an international regulation for general aviation’s emissions, many countries are pushing towards emissions reduction penalising the higher emission aircrafts.
In this context Diesel engines can bring several advantages with respect to conventional gasoline engines in the general aviation field such as:
• Significant fuel consumption reduction, estimated around 30%
• Good suitability for turbocharging with consequent high specific power and capability to keep the performance constant with the altitude
• High torque even at low speed with positive results in terms of gearbox weight reduction
• Robustness, reliability and longer maintenance intervals
• Wider availability of diesel fuel (or JP-8) in comparison with gasoline for general aviation
Moreover the powertrain hybridization can enable further fuel consumption benefits thanks to the engine downsizing as well as zero emissions operating modes as green taxi. Finally, safety could also be increased thanks to the capability of the hybrid powertrain to assist the emergency glide in case of engine failure.
ARTEMIS (Automotive PEMFC Range extender with high TEMperature Improved meas and Stacks) is a collaborative project the aim of which is the development of new high temperature PEMFC (Proton Exchange Membrane Fuel Cell) for operation up to at least 130 °C and their validation in a stack for automotive application as a range extender for electric vehicles.
Moreover, the usage of hydrogen as a fuel for the PEMFC can allow zero emissions operation of the vehicle even when the on-board power source is switched on for range extension.
The main target of the iDea project is the development of an innovative Diesel Engine compliant with future CO2 emission regulations and which could be integrated in a multi-modal hybrid architecture.
The project is mainly divided into two research activities: the first concerning the internal combustion engine, the second dealing with the development of the hybrid powertrain and the optimization of its energy management system.
The main purpose of this research program is the development of a modular hybrid architecture suitable for urban buses (from 6 to 18 m) already equipped with conventional powertrains.
Moreover the project aims to design a revamping platform to update vehicles currently equipped with Euro 0–1–2 engines to buses with a serial hybrid power packs.
Finally the performance of the revamped vehicle will be evaluated in real world driving conditions through the remote monitoring of a small fleet of hybrid busses.
The SOFTECOP research project is focused on the analysis of the potential of the use of raw vegetable oils as fuels for large stationary diesel engines for combined heat and power generation (CHP) and District Heating (DH).
In this way, several powerful actions aiming to reduce fossil fuels consumption and greenhouse emissions will be combined, maximizing their benefits.
Since previous research activities have identified the sunflower as the most suitable vegetable crop for this application in the Piedmont area, a complete analysis (i.e. from “cradle to grave”) is being carried out, starting from the selection of the most appropriate seed from different cultivars and from testing for growth and germinability, which is being carried out by the UNITO research group. Then, after selected seed have been given to local farmers for crop production, and after oil extraction, a large stationary diesel engine installed in a CHP power plant for district heating operated by Ecotermica has been modified to run on SunFlower raw Oil (SFO), and the impact of the use of SFO on the combustion and pollutant emission formation (NOx, PM, UHC) is being deeply analyzed by the POLITO DENER and DISMIC research groups, in order to find out the most suitable engine set-up and calibration.
Finally, the analysis will be completed by comparing the CHP and DH economic and energetic results which can be obtained with SFO with the corresponding results which can be obtained with more traditional CHP plants which are usually operated with fossil fuels (i.e. natural gas), aiming to point out not only the potential benefits in terms of reduction of fossil fuels consumption and greenhouse emissions, but also to assess the economic sustainability for the use as fuels of some particular crops, such as sunflowers, which can represent an interesting option for the agricultural need of crop rotations.
The proposed research program follows and deepens the theoretical and experimental activity carried out in previous national research programs (PRIN 2004 and PRIN 2007), in order to develop methodologies for the optimization of the combustion process in automotive diesel engines fuelled with biodiesel blends, with a special focus on new generation biofuels.
The engine under test will be a small displacement (1300 cm3) automotive diesel engine, equipped with a single stage turbocharger and with a last generation Common Rail fuel injection system, with an aftertreatment system featuring a Close Coupled Diesel Oxidation Catalyst (DOC) integrated with a Diesel Particulate Filter (DPF).
The experimental investigation will be carried out by fuelling the engine with different biodiesel fuels, including FAME (Fatty Acid Methyl Ester) currently available on the European market, biodiesel obtained from Jatropha oil, and finally last generation biodiesel obtained from algae that will be made available during the research activities by the Research Unit of University of Rome Tor Vergata.
After the development of the most suitable engine control strategies to reduce exhaust emissions, combustion noise and fuel consumption, the problems connected to DPF regeneration will be tackled, since the usage of high biodiesel shares in the blend is expected to further complicate the regeneration process, especially at low engine loads and speeds which are typical of urban driving conditions. Moreover, the impact of the different biodiesel fuels on Particulate Matter will be carefully analyzed, both in terms of particle number and in terms of chemical characteristics.
Finally, technologies for the detection of the biodiesel share in the blend and for the automatic adaption of the engine calibration to the fuel blend characteristics will be developed, in order to contribute to provide to the research institutes and to the automotive industries technologies enabling in the next future the diffusion of “flex fuel” engines also for diesel automotive engines (as for the flex fuel spark ignition engines which are nowadays currently available on the market)
The research program follows and deepens the theoretical and experimental activity started with a previous national research program (PRIN 2004) on the optimization of the combustion process when the engine is running with diesel/biodiesel fuel mixtures. The engine under test is a 4 cylinder, 4 valve-per-cylinder, 1300 cm3 displacement, direct injection Common Rail Diesel engine equipped with variable geometry turbocharger, and cooled EGR.
The Design of Experiment (DoE) techniques are being exploited to determine different optimization methodologies for the combustion process of unconventional fuel mixtures, using appropriate engine control strategies to reduce exhaust emissions, combustion noise and fuel consumption. Along with the experimental research activity, numerical simulation and CFD analysis of the in-cylinder spray formation and evaporation is performed, to evaluate the effects of different diesel/biodiesel fuel mixtures on the fuel/air mixing and on the combustion evolution.
The main results of the research activity are the increase of the know-how on the optimization of the control parameters and tuning of high speed Diesel engine running with diesel/biodiesel mixtures. These results will provide to the industrial and academic researchers new strategies and tools for the optimization of spray strategies, of boost and EGR control and of the combustion process in order to reduce exhaust emissions, fuel consumption and combustion noise of Diesel engines when running with non-conventional fuels.
The project aims to define a methodology for the optimization of the calibration of small common rail diesel engines, with focus on multiple injections, through an extensive theoretical and experimental activity.
Optimizations are performed on numerical models of the engines, that are then validated with experimental investigations.
The definition of a proper objective function (due to the complexity of the system response) and the selection of the most effective search method for optimum calibration are the main challenges within this project.
Results of the activity include the definition of effective Design of Experiments and Genetic Optimization techniques for small high-speed Diesel engines, as well as the creation of a wide experimental data-base for numerical models validation.